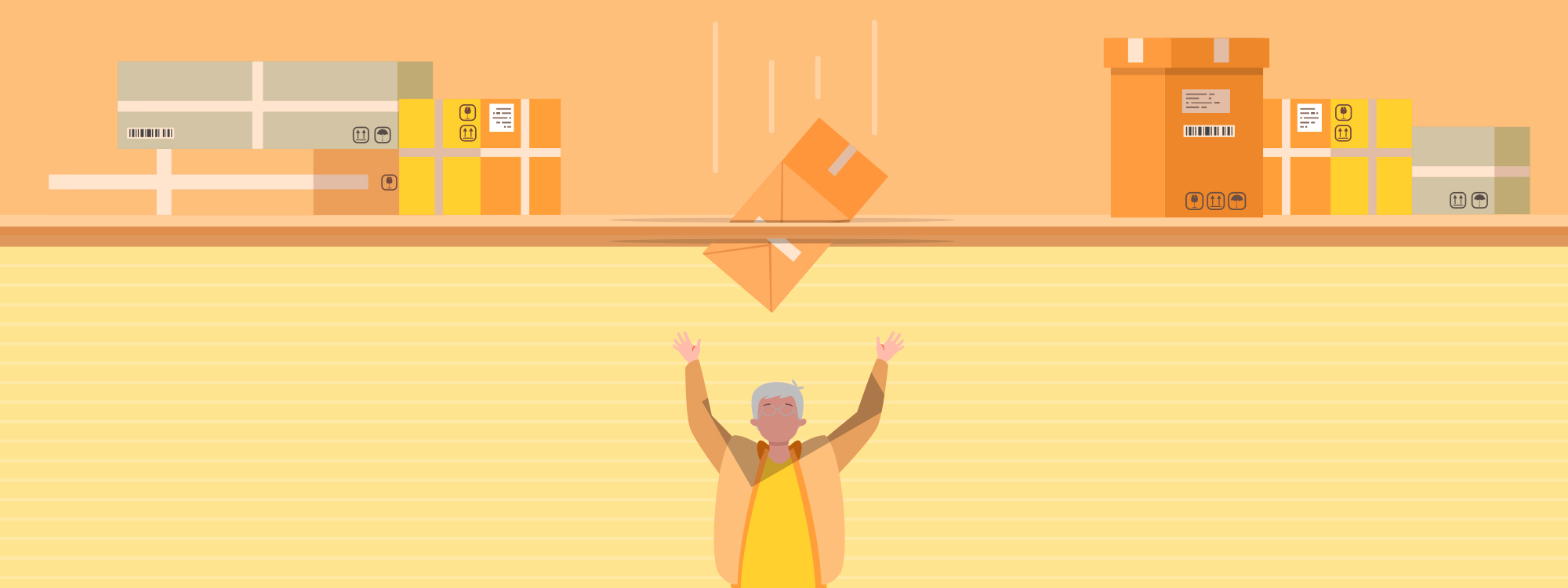
Has a customer ever walked into your store, looking to buy something specific you normally sell, but you’ve sold out? Or, have you ever found yourself drowning in unnecessary surplus inventory because you ordered too much? Well, we hate to break it to you, but you probably need to improve your stock control system.
We’ve put together a short guide detailing what great stock control looks like, common stock control problems you should look out for, different stock control methods you can try, and how to perform stock counts like a pro. So, you’ll never find yourself having to wrangle with poor stock management ever again. Let’s get started.
- What is stock control?
- What are common stock control problems?
- Different types of stock control systems
- How to count inventory
Track inventory levels and SKUs. Order new stock directly from Lightspeed Retail. Avoid out-of-stocks with reorder points and low stock alerts. And, much, much more.Optimise Your Inventory Management. With Lightspeed Retail
What is stock control?
Stock control, or inventory control, is the process of managing how much stock you have, and how you keep track of it. This covers tracking the movement of stock from the point of purchase, warehousing, moving goods to your retail store, or shipping them to your customers, and finally, re-ordering the stock.
Good stock control means that the right amount of stock is available, at the right place, at the right time. This ensures that capital is not tied up with surplus stock (overstocking), and that you don’t run out of stock in times of need (understocking). We’ll cover the different types of problems poor stock control brings down below.
What are common stock control problems?
If you don’t have an effective stock management process in place, you’re likely to run into some logistical issues later down the road. We’re sure you’ve heard the expression: “Fail to prepare, prepare to fail’? Well, there’s no situation more appropriate than poor stock management to use that expression.
We’ll run through some of the more common problems you’re likely to experience if you don’t have a good stock control system in place.
Overstocking: This is when a business has more inventory than it can sell. This can produce a few different issues, depending on the stock in question. Most retailers can experience:
- Increased storage costs to hold the surplus inventory, if they are using a warehouse, or reduced capacity to store inventory.
- Inventory obsolescence which is where products eventually become obsolete if they are not sold quickly enough. Imagine you’re an electronics retailer who has surplus stock of iPod Touch’s. There may be some diehard Apple fans that pick a few up, but generally, it would be considered obsolete stock.
- Product deterioration if you’re stocking perishable items such as food and beverages. Clothing is even susceptible to deterioration depending on the environment in which it is stored. Light, temperature, and humidity, for example, can all contribute to a textile’s health or deterioration, depending on their intensity.
- Reduced cash flow as you will have large portions of cash tied up in stock that could potentially be deteriorating in either quality, or relevancy, over time.
Understocking (Stockouts): This is when a business doesn’t have enough inventory to meet customer demand. This can result in:
- Lost sales if a business doesn’t have enough inventory for a particular item in high demand.
- Customer dissatisfaction as a result of customers being unable to purchase a product they’re looking to buy. This can have ripple effects, especially if this becomes a recurring issue, with customers being turned off your business as they see you as unreliable which, in turn, affects brand reputation.
Poor stock visibility: This is when a business doesn’t have a clear view of its stock levels. This normally leads to the aforementioned issues of overstocking or understocking as purchasing stock effectively becomes guess work.
Poor stock visibility tends to be more common when retailers are performing manual stock counts rather than relying on inventory management software, which provides far greater oversight of how much stock you have, for any particular item, at any given time.
Track inventory levels and SKUs. Order new stock directly from Lightspeed Retail. Avoid out-of-stocks with reorder points and low stock alerts. And, much, much more.Optimise Your Inventory Management. With Lightspeed Retail
Inventory shrinkage: This refers to lost inventory for reasons other than sales. The amount of inventory a business has available is different to the amount of inventory that it should have available (according to a business’ stock records). This can happen for a number of reasons including:
- Product theft from either employees, customers, or suppliers
- Product damage usually due to damage sustained during transit, storage, or handling by employees, customers, or suppliers
- Product loss usually due to human errors or natural disasters
- Administrative errors due to issues sustained in inventory counts, or processing orders.
Inventory shrinkage can create problems with your stock control as you can find yourself having less stock than you initially intended, i.e., understocking. This can result in lost sales, and resultantly, reduced profits.
In summary, retailers generally fall into problems with poor stock control due to poor demand forecasting (where a business overestimates, or underestimates, demand for a product), poor inventory management, unexpected changes in demand, and supply chain disruptions.
Different types of stock control systems
There are many different types of stock control systems to choose from. Whilst we won’t be covering all of them, we’ve pulled together some of the most popular, and commonly used, stock control systems you can use. We’ll cover ABC Analysis, First In/First Out, and the Just-in-Time method.
ABC Analysis: ABC analysis determines the value of inventory items into three categories (A, B, and C) based on how important they are to the business. Inventory is valued, and moved into different categories, based on cost, risk, and demand. ‘Category A’ is the highest whilst ‘Category C’ is the lowest.
The ABC analysis system is based on the Pareto Principle. The Pareto Principle, otherwise known as ‘The Law of the Vital Few’, specifies that 80% of results come from 20% of causes. So, 20% of stock generally makes up 80% of all value. This is why inventory items are categorised as A, B, or C, depending on how valuable they are to your business. Here’s a general example:
- Category A – items that account for 80% of your revenue
- Category B – items that account for 15% of your revenue
- Category C – items that account for 5% of your revenue
Benefits of ABC Analysis:
- Improved inventory optimisation: Categorising your inventory based on demand, cost, and value to your business will enable you to have greater oversight of what you should keep more of, and what you should keep less of. Save warehousing space and, even, the risk of overstocking less in-demand items you sell.
- Greater profits: Conducting an ABC analysis can help you identify your most in-demand items. If you have certain items that are in great demand, this can allow you to gently increase the price and, resultantly, your profits. Of course, we’re not suggesting increasing prices to astronomical levels. But, it won’t hurt to raise the prices slightly for something that is in great demand.
First In, First Out Method: The First In, First Out (FIFO) method requires that whatever stock has been purchased first, must be sold first. The general idea is that the FIFO method creates a pipeline that means that older inventory gets shipped out before newer inventory gets shipped in. This is also really useful for accounting, as the prices and values of each piece of inventory is accurate as it can be. This is because the stock isn’t sitting around too long, potentially becoming obsolete, and retaining its value.
FIFO is one of the easiest and most accurate ways to calculate inventory value whilst also being incredibly efficient at removing the risk of overstocking, stock obsolescence, and warehousing costs.
Benefits of FIFO:
- Reduced storage costs: Similar to the JIT method (that we’ll cover below), the FIFO method helps to reduce storage costs. You’re only taking stock in, once you’ve sold your existing stock which can help you manage stock levels and never be over encumbered with surplus inventory.
- Accurate cost analysis: FIFO provides the most accurate view, out of all the stock control methods, of what your inventory is costing the business at any given time (as we discussed above). This helps improve accounting, and allows you greater control and visibility of your liquidity.
Just-in-Time Method: The Just-in-Time (JIT) method requires that inventory is only received when a business needs it. This ensures that there is enough stock on hand to deal with demand, whilst also not holding stock that is surplus to a business’ requirements. So, you purchase your inventory for suppliers as and when you need it.
For example, if you’re a clothing retailer, and Summer is just around the corner, you would order enough t-shirts, shorts, sunglasses, and other beachwear. You would not, however, hold onto scarves, gloves, woolly hats, and so on, as these are items typically worn around Autumn and Winter.
The JIT method works really well for those who know how to use it well. You need to accurately forecast demand, and monitor your inventory levels in real-time so you ensure that you’re buying the right type of stock and the right amount of stock. Otherwise, you risk having a lot of stockouts.
Benefits of Just-in-Time method:
- Reduced storage costs: If you streamline the amount of stock you have, you’ll notice you need far less warehousing space. Which, ultimately, means your inventory storage costs will be lower.
- Reduced inventory obsolescence: If you have loads of stock on hand, especially items that are seasonal, or dependent on trends, you may increase the risk of your inventory becoming obsolete and going unsold.
How to count inventory
We’ve now covered the different types of stock control you can implement for your retail business. However, this has mainly focused on warehousing and how to optimise your stock levels so you always have enough stock on hand. Let’s now move to your retail store.
If you want to make sure your business isn’t overflowing with stock, or is completely absent of stock, you’ll need to conduct stock counts. There are two main methods for counting inventory: physical inventory counts and cycle counting. Let’s explore the difference between the two.
Physical inventory count: This type of count is when you count all of the products in your retail store in person. This is typically carried out by an assigned member of staff (or team of staff depending on how much inventory there is to count) who will count the inventory levels of each item on the sales floor and in the stockroom.
The team will then manually record inventory levels for each item either with a pen and paper, or electronically using an inventory Excel spreadsheet. Physical inventory counts can be time-consuming and, as a result, most retailers only do them once a year.
Cycle counting: This type of count differs from a physical inventory count because instead of counting all your inventory at once, you count select portions of your inventory on an ongoing basis. This is otherwise known as a partial stock count.
Cycle counting allows merchants to continuously maintain accurate inventory levels without needing to work extra hours. These types of counts should, ideally, be performed every three months. However, it can also be done daily, weekly or monthly. The main benefit is that it prevents you from needing to do full inventory counts any more than you need to.
The choice of which type of count you perform is entirely up to you. However, cycle counting is a lot less time consuming. Plus, it’s a lot less stressful. Rather than having a mammoth task you need to overcome once every single year, you can just stay on top of it on a daily, weekly, or monthly basis.
While counting stock may sound like a very mundane, albeit simple task, there are some strategies you can implement to make the whole process so much smoother.
Use inventory counting technology
Tallying up your inventory with a paper and papers, or an Excel sheet, may get the job done, but it isn’t without pitfalls. You’ll have to enter the data you’ve collected into your ePOS, which requires double entry.
If you’re using an ePOS with built-in inventory management tools, you can reduce the time it takes to count inventory.
With Lightspeed’s Inventory Counts capability, merchants can count, reconcile and compare counts from different time periods using a barcode scanner. Count stock faster, address discrepancies, and assure that the inventory levels in your ePOS system and in your store are the same.
If you’re already using Lightspeed, you can visit our support page on doing inventory counts for a step-by-step walkthrough.
Choose your inventory counters wisely
Stock takes require consistency and attention to detail. Select a seasoned team member that you can trust to take the job seriously and prioritise accuracy.
Inventory counters should be familiar with what you sell and where products are in your store and stockroom. Inventory counting is a good task for more junior team members, who may need to learn the ropes and be relied upon for future stock takes.
If you’re flying solo, third-party inventory counters may be a viable option. They can perform the store-wide counts while you tackle the more manageable cycle counts. You should keep in mind that stock-taking procedures vary from one provider to another, so it’s important to consult the third-party stock taker to get a clearer understanding of their processes and price.
Schedule physical counts in advance
Physical counts can be time-consuming. It’s important to plan ahead and think about when to schedule full counts, and how often. When and how frequently you perform a full stock take varies from one business to another. Some stores do full physical inventory counts once a year, others twice a year, while others carry them out at frequent intervals.
On his blog, Bob Phibbs, The Retail Doctor, mentions that the best times to do a full inventory count are the last weekend of January (during the post-holiday lul) or at the end of July because SKU levels are at their lowest at these times.
In any case, settle your inventory counting schedule well in advance and to notify your stocktaking team so they can make themselves available.
Whenever possible, perform physical counts after business hours. If that’s not an option and you need to close your shop temporarily, let your customers know by email (MailChimp has an email builder that’s simple to use) and with in-store signage. Tell them why you’re closing, when you’ll reopen, and that they can still shop through your online store.
If you’re already using Lightspeed, you can integrate MailChimp with your ePOS system and send personalised emails and recurring newsletters to people subscribed to your mailing list.
Map out your store
Print out a map of your shop and stockroom and make notes as to where each product type is located. A labelled map of your store’s layout makes it easier for you to assign workers to a specific product or section. That way you stay organised and can more easily divide and conquer which inventory is counted and by who.
Bob Phibbs also suggests including “the location of every rack, display, wall, and shelf,” and labelling what product categories are located there.
Your labelled store layout can also serve as a handy checklist throughout the inventory counting process. Once a section is counted and any discrepancies are identified, simply mark it off as completed.
Label boxes and shelves
When it comes to counting inventory, staying organised is key. Stray products without a box or packaging results in avoidable discrepancies and revenue loss.
Keep your stockroom organised by labelling boxes of products that aren’t visible or are hidden and store them by product type (i.e., storing jeans with other jeans). Store your products in defined areas and assure that staff categorise products accordingly, never misplacing items.
Tip: Make sure your products are where they should be before performing a physical inventory count. Walk around your stockroom and sales floor and be on the lookout for stray or misplaced products.
Deal with uncategorised inventory
Before you start a stock take, check your ePOS system’s ‘Uncategorised Inventory’ report to check for any items with no assigned category. Well-organised inventory in your ePOS system will reduce preventable discrepancies, facilitate stock purchasing, and assure the accuracy of future ‘Inventory Count’ reports you may refer to.
If you’re already using Lightspeed, you can address uncategorised inventory before a stock take with the ‘Uncategorised Inventory’ report.
Find the right stock control system for your business
Stock control and inventory counting are processes you learn by doing. All businesses are unique, so you’ll likely cycle through some different methods before landing on one that fits your specific needs.
However you do it, make sure you have the right tools to make you and your team’s lives easier. Want to know Lightspeed can help? Watch our free Lightspeed Retail demo here.
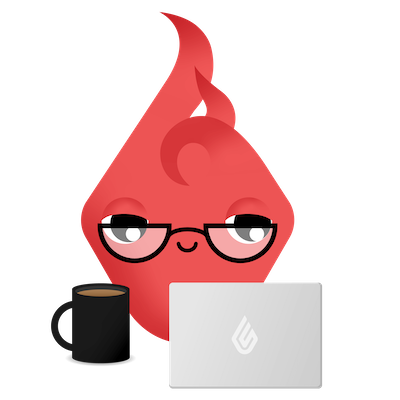
News you care about. Tips you can use.
Everything your business needs to grow, delivered straight to your inbox.